No More Worries!
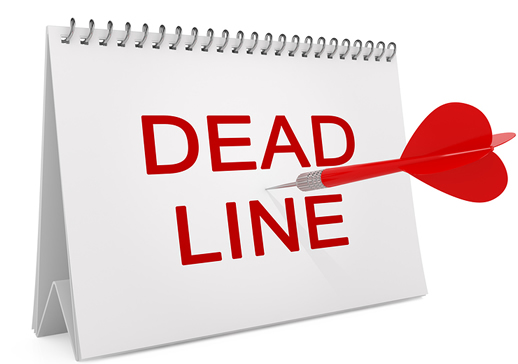
Paper Formatting
- Double or single-spaced
- 1-inch margin
- 12 Font Arial or Times New Roman
- 300 words per page
No Lateness!

Our Guarantees
- Free Unlimited revisions
- Guaranteed Privacy
- Money Return guarantee
- Plagiarism Free Writing
Applying the Finite Element Method to Solve Complex Engineering Problems
How do you apply the finite element method to solve complex engineering problems?
Sample Answer
Applying the Finite Element Method to Solve Complex Engineering Problems
Introduction
The Finite Element Method (FEM) is a powerful numerical technique widely used in engineering for solving complex problems involving structural, thermal, fluid, and electromagnetic analyses. FEM allows engineers to break down intricate geometries and material behaviors into manageable elements, enabling precise calculations of physical phenomena. This essay outlines the steps involved in applying the finite element method to engineering problems, highlights its significance, and discusses its applications across various fields.
Understanding the Finite Element Method
The Finite Element Method involves subdividing a large system into smaller, simpler parts called finite elements. By solving these elements collectively, engineers can approximate the behavior of the entire system. The fundamental steps in applying FEM include:
1. Discretization of the Domain
2. Selection of Element Type
3. Derivation of Element Equations
4. Assembly of Global System Equations
5. Application of Boundary Conditions
6. Solution of the System of Equations
7. Post-Processing
1. Discretization of the Domain
The first step in applying FEM is to discretize the geometry of the problem domain into a mesh of finite elements. The mesh can consist of various shapes (triangles, quadrilaterals, tetrahedra, etc.) depending on the dimensionality (2D or 3D) and complexity of the geometry.
– Mesh Quality: The quality of the mesh significantly impacts the accuracy and convergence of the solution. Finer meshes yield more accurate results but require more computational resources.
2. Selection of Element Type
Different types of elements are available for modeling various physical phenomena. The choice of element type depends on factors such as:
– Dimensionality: 1D (line), 2D (plane), or 3D (solid).
– Behavior: Linear or nonlinear material models.
– Application: Structural analysis, heat transfer, fluid dynamics, etc.
Commonly used elements include linear and quadratic elements for solid mechanics, shell elements for thin-walled structures, and beam elements for structural members.
3. Derivation of Element Equations
Once the mesh is created and element types are selected, the next step is to derive the governing equations for each element. This often involves:
– Utilizing variational principles (e.g., the principle of minimum potential energy) or weighted residual methods.
– Formulating element stiffness matrices and force vectors based on material properties and loading conditions.
For linear static problems, the governing equation is typically expressed in matrix form as:
[
\mathbf{K} \mathbf{u} = \mathbf{F}
]
where ( \mathbf{K} ) is the global stiffness matrix, ( \mathbf{u} ) is the displacement vector, and ( \mathbf{F} ) is the force vector.
4. Assembly of Global System Equations
After deriving individual element equations, they are assembled into a global system by combining all element contributions based on shared nodes. This step results in a large system of equations representing the entire model.
– Global Matrix Assembly: Care must be taken to accurately assemble the global matrices while maintaining continuity at shared nodes between elements.
5. Application of Boundary Conditions
Boundary conditions are critical for ensuring that the model accurately represents the physical constraints and loading conditions:
– Essential Boundary Conditions: These define specific values for displacements at certain nodes (e.g., fixed supports).
– Natural Boundary Conditions: These define forces or pressures acting on the boundaries (e.g., applied loads).
Incorporating boundary conditions modifies the global system of equations appropriately.
6. Solution of the System of Equations
The next step involves solving the assembled system of equations using numerical techniques such as:
– Direct solvers (e.g., Gaussian elimination).
– Iterative solvers (e.g., conjugate gradient methods).
The chosen solution method should consider factors such as problem size and computational efficiency.
7. Post-Processing
After obtaining the solution, post-processing is performed to interpret and visualize results:
– Displacement Visualization: Plots showing displacement contours or deformed shapes provide insights into structural behavior.
– Stress Analysis: Calculating stress and strain distributions helps assess material performance under loading conditions.
– Verification and Validation: Comparing results with analytical solutions or experimental data ensures accuracy and reliability.
Applications of Finite Element Method in Engineering
FEM has a broad range of applications across various engineering disciplines:
1. Structural Analysis: Evaluating stresses and deformations in beams, frames, and complex structures under various loading conditions.
2. Thermal Analysis: Modeling heat transfer problems in solid bodies to optimize thermal management in electronic devices or machinery.
3. Fluid Dynamics: Analyzing fluid flow in pipes, channels, and around objects (CFD applications).
4. Electromagnetic Fields: Solving problems related to electric and magnetic fields in devices like transformers and motors.
5. Biomechanics: Studying biomechanical behavior in biological tissues for medical device design or surgical planning.
Conclusion
The Finite Element Method is an essential tool in engineering for solving complex problems across various domains. By discretizing domains into finite elements and systematically assembling equations, engineers can analyze intricate structures and systems with greater accuracy. The versatility and robustness of FEM make it a cornerstone technique in modern engineering analysis, enabling advancements in design, optimization, and safety across numerous applications. As computational capabilities continue to evolve, FEM will remain a key component in tackling increasingly complex engineering challenges.
This question has been answered.
Get AnswerPrice Calculator
12% Discount
- Research Paper Writing
- Essay Writing
- Dissertation Writing
- Thesis Writing
Why Choose Us
- Money Return guarantee
- Guaranteed Privacy
- Written by Professionals
- Paper Written from Scratch
- Timely Deliveries
- Free Amendments